微型钻头作为精密加工领域的关键工具,其直径通常在0.1至0.5毫米之间,其螺旋槽的加工质量直接影响到钻孔精度和使用寿命。由于砂轮在磨削过程中形成的微观廓形尺寸极小(通常为微米级),传统的检测手段难以满足精度和效率要求。这一技术瓶颈长期制约着微型钻头制造的良率提升和工艺优化。本文将从技术现状、核心挑战、创新解决方案及未来发展方向四个方面,系统探讨砂轮微观廓形检测的实现路径。
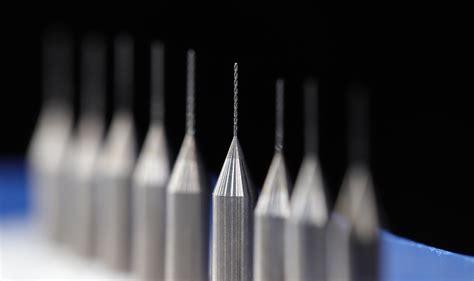
一、现有检测技术的局限性分析
传统检测手段主要依赖接触式探针测量和光学显微成像。接触式三坐标测量机(CMM)的探针尖端直径通常在50微米以上,远超检测目标的特征尺寸,存在物理接触导致的测量误差和表面损伤风险。光学显微镜虽能实现非接触观测,但受限于光学衍射极限,理论分辨率仅能达到0.2微米左右,实际应用中因景深限制和表面反光特性影响,难以准确重构三维廓形。电子显微镜虽具有纳米级分辨率,但需真空环境和复杂样品制备,检测效率低且设备成本高昂,无法适应工业现场需求。
二、微观廓形检测的核心技术挑战
1.亚微米级分辨率需求:砂轮修整区域的特征尺寸普遍在5-50微米范围,表面粗糙度要求达到Ra<0.1μm,需要检测系统具备亚微米级空间分辨能力。
2.三维形貌重构难题:螺旋槽的几何精度涉及复杂三维轮廓参数,包括前角、后角、刃带宽度等,传统二维成像无法完整表征。
3.动态检测适应性:在线检测需适应砂轮高速旋转(通常>10,000rpm)工况,消除运动模糊对成像质量的影响。
4.环境干扰抑制:加工现场存在的冷却液雾化、金属碎屑等污染物,对光学系统构成严重干扰。
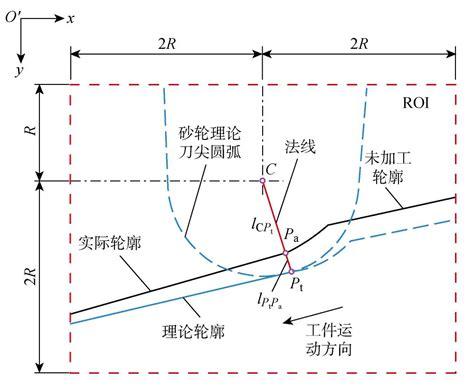
三、创新性解决方案探索
(一)超分辨光学检测技术
采用结构光照明与计算成像相结合的方案突破光学衍射极限。通过设计特定空间频率的条纹投影系统,配合相移算法和频域解调技术,可将横向分辨率提升至λ/4(约100nm)。采用高数值孔径物镜(NA>0.9)和蓝光光源(λ=405nm)可进一步优化分辨能力。关键技术创新点在于:
多模态照明系统:交替使用暗场、微分干涉(DIC)照明模式,增强边缘对比度
自适应对焦算法:基于图像清晰度评价函数的实时反馈控制,补偿砂轮轴向跳动
深度学习去噪:训练卷积神经网络(CNN)消除冷却液残留造成的图像伪影
(二)共聚焦显微测量技术
线扫描共聚焦系统通过轴向扫描获取三维表面形貌数据,纵向分辨率可达10nm。针对砂轮检测的特殊需求,可改进为:
高速振镜扫描:采用MEMS微镜实现kHz级扫描频率,单次测量时间<0.1s
多光谱探测:利用不同波长光的穿透深度差异,区分表面污染层与真实形貌
相位解包裹算法:解决高陡坡区域相位跳变问题,精确重构螺旋槽侧壁角度
(三)激光干涉测量创新
开发基于数字全息干涉术(DHM)的在线检测系统。将砂轮表面反射的物光波与参考光波干涉,通过傅里叶变换重建三维相位分布。关键技术突破包括:
同轴光路设计:消除离轴像差,适应曲面测量
脉冲激光光源:采用ns级脉冲宽度冻结砂轮旋转运动
相位解调优化:结合四步相移法和空间载波技术,实现单次曝光三维测量
(四)智能数据分析体系
构建"数据采集-特征提取-质量评估"的全链条智能分析平台:
1.多源数据融合:集成光学、声发射、力信号等多模态传感数据
2.数字孪生建模:建立砂轮-工件交互过程的物理仿真模型,实现虚拟测量
3.异常检测算法:采用孤立森林(Isolation Forest)算法识别微观廓形偏差
4.自学习补偿系统:通过强化学习动态调整砂轮修整参数
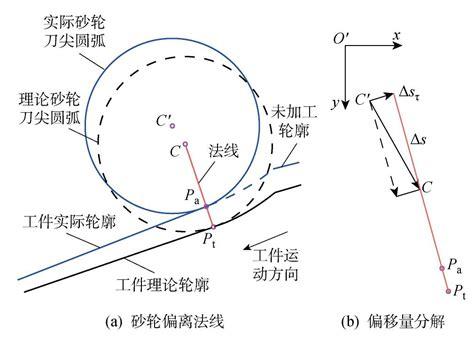
四、工程化实施路径
1.模块化系统设计:将检测单元集成到数控磨床内部,采用工业机器人实现自动上下料
2.环境控制子系统:集成气幕隔离装置和真空吸附系统,维持检测区域洁净度
3.在线校准机制:设置标准样板定期进行系统标定,补偿温度漂移误差
4.人机交互界面:开发AR可视化系统,实时显示三维点云数据与公差带对比
五、技术经济性分析
以某型号0.3mm微型钻头生产线为例,实施该检测系统后:
检测周期从传统抽样检测的2小时缩短至在线全检的15秒/件
良品率由78%提升至95%以上
砂轮使用寿命延长40%,年节约成本约120万元
设备投资回收期约1.8年
六、未来发展方向
1.量子传感技术应用:探索基于NV色心的量子精密测量,实现纳米级磁场分布检测
2.片上集成检测系统:研发MEMS工艺制造的微型化传感器阵列
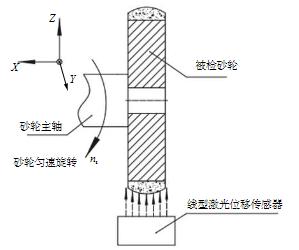
1.跨尺度关联分析:建立微观廓形特征与宏观加工质量的映射关系模型
2.自主修复材料研究:开发具有自锐功能的智能砂轮材料
砂轮微观廓形检测难题的突破需要多学科交叉创新,既要提升传感技术的极限性能,又要构建智能化的数据分析体系。通过光学超分辨、计算成像、人工智能等技术的深度融合,结合精密机械设计与工业物联网架构,有望建立适应微细加工需求的智能检测闭环系统。这不仅将推动微型钻头制造技术的进步,对精密医疗器械、微电子封装等领域的工艺革新也具有重要借鉴意义。